What Is Cold Chamber Pressure Die Casting?
Cold chamber pressure die casting refers to a metal casting process where molten metal under high pressure is confined within the die by the force of gravity. The shape of the die cavity determines what shape the final part can be.
The molten metal then solidifies as it cools and drains from within the mold. This type of casting process is widely used in the production of components for aircraft, space vehicles, and infrastructures, such as buildings and roads. The most common term for this process is mold casting. The process is simpler than other types of casting methods such as sand casting or lost-wax casting because the material is not spread from a spinning pot as with sand or clay.
What are the advantages of cold chamber pressure die casting?
- Processing costs are lower than open-die casting
The reason is that it generally requires less metal to fill the mold cavity. Also, there is no need for a supporting flask, which lowers the cost of this type of casting. According to Eko Industries , this occurs because the high pressure is within the die itself, rather than in a flask. Also, the process is cleaner since no sand or clay particles are created during casting. Standards for cold chamber pressure die casting are more closely controlled than with other methods, such as sand casting or lost-wax casting which can allow variations between different molds.
- Fewer chances of defects
The risks of producing defects in the cast products are lower because cold chamber pressure die casting has greater dimensional accuracy than open-die casting. Since there is no sand or clay involved, the die cavity and mold are completely separated. The molten metal can flow more easily because of the smaller inner diameter of the die.
- It is more environmentally friendly
This type of casting requires less energy than other types of casting methods because it takes place in a closed system within a die rather than in an open flask. Another advantage is that there are no flasks or molds required, which significantly decreases transportation costs.
How is cold chamber pressure die casting performed?
Cold chamber pressure die casting is safer than other casting methods because there are fewer parts to produce and no sand or clay medium to handle. Also, when compared with sand casting or clay parting, it is more environmentally friendly as the liquid metal and the mold is completely separated inside the cavity. Moldmaking professionals and engineers use a variety of tools for this process depending on the type of geometry needed for each part. Certain standard molds allow for the production of certain types of parts.
Conclusion
As you can see, the casting process is pretty simple. The die and the mold are separated by a partition. The molten metal is poured into the cavity through a sprue and then solidifies. Because of this process, you have to choose a material that can withstand high temperatures because this is going to be a major factor in your final decision as it may not allow your product to be made using any other type of process.
Also Read – Understanding Everything About Energy Conservation
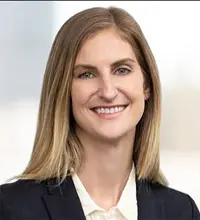
Caroline is a dedicated writer with a passion for keeping readers informed. Specializing in providing the latest news updates and unbiased reviews, she strives to deliver accurate and insightful content. With a keen eye for detail and a commitment to journalistic integrity, Caroline ensures that her readers are always well-informed. Stay tuned for her latest articles to stay up-to-date on current events and trends.